Sink or Swim: Mastering Your Bilge Pump Wiring (Rule 1100)
Ever been ankle-deep in unwanted water on your boat? A sputtering, unreliable bilge pump can quickly turn a relaxing day on the water into a frantic bailing session. Don't let a faulty setup sink your fun – and potentially your wallet. Understanding the intricacies of bilge pump wiring, particularly in line with ABYC Rule 1100, is crucial for any boat owner.
ABYC Rule 1100 outlines the standards for electrical systems in small craft, including critical components like bilge pumps. While “Rule 1100 bilge pump wiring” isn’t a specific standalone regulation, the broader standard dictates proper installation and configuration for these vital systems. Ignoring these guidelines can lead to malfunctions, premature pump failure, and even dangerous electrical hazards.
Historically, bilge pump systems were simpler, but as boats have become more complex, so too have their electrical demands. Rule 1100, maintained and updated by the American Boat and Yacht Council (ABYC), helps to ensure safety and reliability in these intricate systems. The importance of adhering to these guidelines cannot be overstated. A properly wired bilge pump system is your first line of defense against flooding, protecting your investment and ensuring the safety of everyone on board.
Understanding the core principles of Rule 1100 as they apply to bilge pumps involves focusing on proper wire sizing, fuse protection, switch placement, and overall circuit design. Correct wire sizing ensures efficient power delivery to the pump, preventing overheating and potential fires. Fuses act as safety valves, breaking the circuit in case of a short, preventing damage to the pump and other electrical components. Properly located switches allow for easy access and control of the pump, whether automatic or manual.
Imagine this: You're miles offshore, and your automatic bilge pump fails because of a corroded wire connection – a direct result of improper installation. Now you’re faced with a potentially dangerous situation. Adhering to Rule 1100 for your bilge pump wiring helps avoid these scenarios. It's not just about compliance; it’s about peace of mind, knowing your system is designed to function reliably when you need it most.
Benefits of complying with Rule 1100 for bilge pump wiring include enhanced safety, improved pump longevity, and reduced risk of electrical system failures. By using correctly sized wiring and fuses, you minimize the risk of fires and ensure efficient pump operation. Correct installation and regular maintenance extend the lifespan of your pump, saving you money in the long run.
A simple action plan for a Rule 1100 compliant bilge pump setup involves: 1) Consulting the ABYC standards, 2) Selecting appropriately sized wiring and fuses, 3) Installing a dedicated circuit for the pump, and 4) Regularly inspecting and testing the system.
Advantages and Disadvantages of Adhering to Rule 1100 Bilge Pump Wiring Guidelines
Advantages | Disadvantages |
---|---|
Increased safety and reduced risk of electrical hazards | Initially higher cost due to quality components and potential labor |
Improved reliability and longevity of the bilge pump system | Requires more time and effort for proper installation |
Peace of mind knowing the system meets industry standards | May require specialized tools and knowledge |
Frequently Asked Questions:
1. What wire size should I use for my bilge pump? (Consult ABYC standards and your pump manufacturer's recommendations.)
2. Where should I place the bilge pump switch? (Easily accessible location.)
3. How often should I test my bilge pump? (Regularly, at least monthly.)
4. What type of fuse should I use? (Consult ABYC standards and your pump manufacturer's recommendations.)
5. Can I wire my bilge pump directly to the battery? (Not recommended; use a properly fused and switched circuit.)
6. What is the purpose of a float switch? (Automatically activates the pump when water reaches a certain level.)
7. How can I prevent corrosion in my bilge pump wiring? (Use marine-grade wiring and connectors, and regularly inspect for signs of corrosion.)
8. What are the signs of a failing bilge pump? (Slow pumping, excessive noise, frequent cycling.)
Tips and tricks: Use marine-grade wiring, connectors, and heat shrink tubing. Double-check all connections and ensure proper grounding. Regularly inspect your bilge pump system for signs of wear and tear, and replace any worn components promptly. Consider installing a high-water alarm for added safety.
Ensuring your boat stays afloat is paramount. Understanding and implementing proper bilge pump wiring according to ABYC Rule 1100 provides a crucial layer of protection against flooding and potential disaster. While it may require an initial investment of time and money, the long-term benefits of a reliable bilge pump system far outweigh the costs. Don't skimp on safety – invest in a robust, properly wired bilge pump system today, and enjoy countless worry-free days on the water. A little preventative maintenance and adherence to industry standards will save you from headaches, potential hazards, and ultimately, keep your vessel afloat and your adventures sailing smoothly. So, take the time to understand the guidelines, implement best practices, and ensure your bilge pump is always ready to handle whatever the waters throw your way.
Unlocking the world of videos for 5 year olds a parents guide
Conquering the p0010 code a comprehensive guide
The rise of ski mask dope art rebellion anonymity and artistic expression


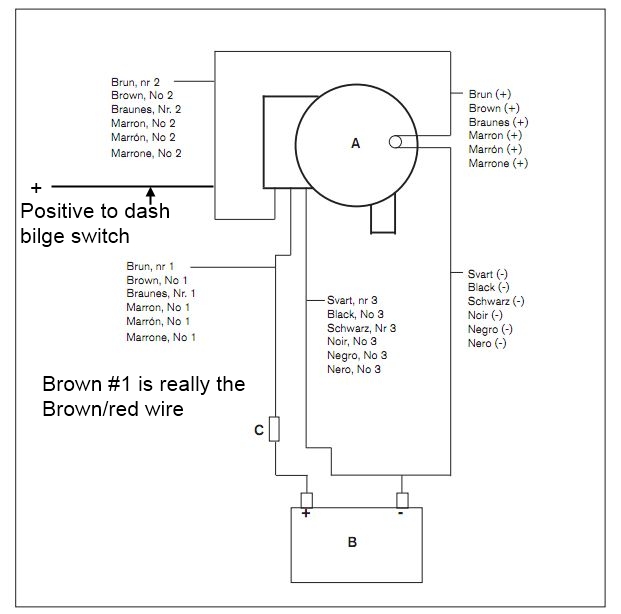









